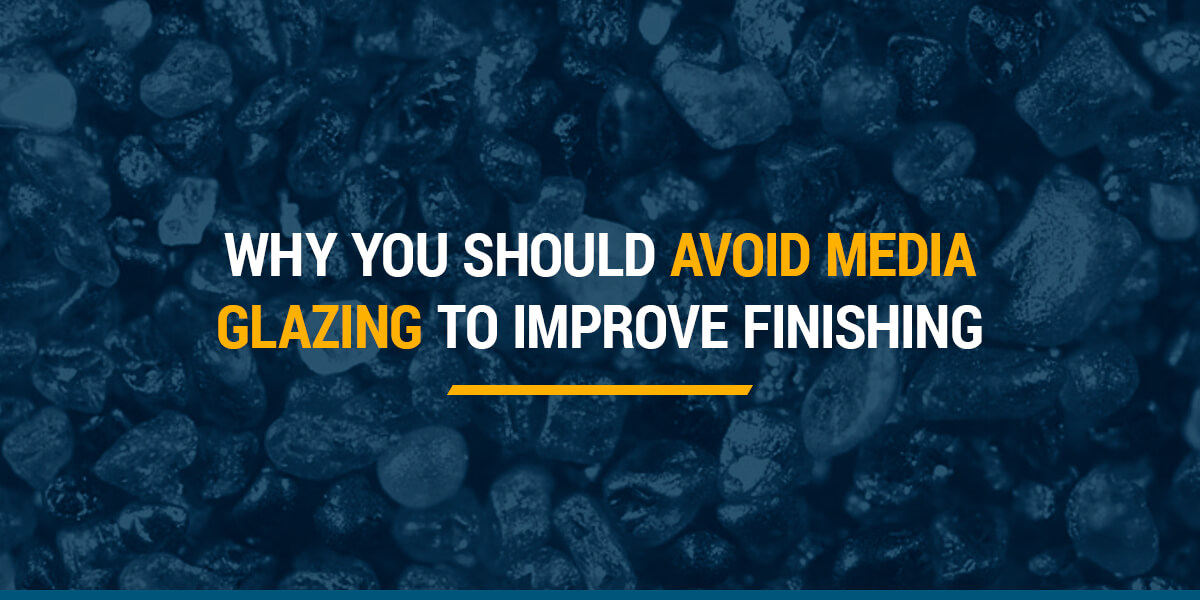
Why You Should Avoid Media Glazing to Improve Finishing
Updated: March 12, 2024Abrasive media plays a crucial role in surface finishing across various industries. From deburring and polishing to cleaning and burnishing, different types of media—such as ceramic, plastic, and steel—are used to achieve the desired finish on workpieces. However, over time, media can become glazed, which significantly reduces its effectiveness. This issue can lead to inconsistent results, longer cycle times, and even rework. Understanding what causes media glazing and how to prevent it is essential for maintaining high-quality finishes that meet your customers' expectations.
What Is Media Glazing?
Media glazing occurs when fine metal particles and debris from the workpiece accumulate on the surface of the abrasive media during the finishing process. This buildup happens due to friction caused by the vibratory action in the finishing machine. As a result, the media loses its cutting ability and becomes less effective at achieving a consistent finish. Instead of removing burrs or smoothing surfaces, glazed media may leave behind a burnished or uneven appearance. In some cases, it can even transfer contaminants from the media to the workpiece, further compromising quality.
The consequences of media glazing are far-reaching. It not only affects the final finish but also increases cycle times, leading to inefficiencies in production. By avoiding glazing, you can maintain smoother workflows, reduce downtime, and ensure better consistency in your finishing operations. The key to success lies in understanding the factors that contribute to this issue and taking proactive steps to prevent it.
What Causes Glazing?
Several factors can lead to media glazing, including:
- Compound concentration: Using too little compound can prevent the media from being properly cleaned, increasing the likelihood of glazing.
- Water flow: Insufficient water flow fails to flush away metal particles and debris, allowing them to build up on the media.
- Part-to-media ratio: A high ratio, especially with oily or greasy parts, can accelerate glazing.
- Media size: Small media can clog drains and trap dirty water, leading to surface contamination.
These variables interact in complex ways, so it's important to monitor and adjust them regularly to maintain optimal performance.
6 Tips to Prevent Media Glazing
Preventing media glazing starts with proper setup and maintenance. Here are six practical steps you can take:
1. Use the Right Compound for Your Material and Equipment
Soft materials like copper, brass, aluminum, and certain types of steel are more prone to glazing. Choosing the correct compound for your specific application ensures better cleaning and prevents buildup. An improper compound can lead to poor results and increased wear on the media.
2. Maintain the Correct Compound Concentration
Compound concentration is critical. Too low, and the media won’t clean effectively, leading to glazing. Aim for a concentration between 0.7% and 1%, depending on the system’s capacity and water volume. Proper dosing improves efficiency and reduces cycle times.
3. Keep Drains Clear and Free of Clogs
Clogged drains can cause water retention, which leads to media contamination. Ensure your drains are open and functioning correctly. If closed drains are required, replace the water frequently to avoid soil buildup.
4. Ensure Adequate Water Flow
Good water flow helps remove debris and keeps the media clean. Open drains with sufficient flow produce the best results, reducing the chance of glazing and improving overall finish quality.
5. Monitor Your Wastewater Stream
Dark or concentrated wastewater is a sign of potential glazing issues. This often happens when working with low-quality materials, high part-to-media ratios, or parts with heavy oil or grease. Regularly inspect your media and consider process audits if needed.
6. Check and Replace Media as Needed
Over time, media degrades and becomes smaller, which can lead to clogging and glazing. Implement regular checks and replace any media that shows signs of wear or contamination. This helps maintain consistent performance and extends the life of your media.
How to Restore Glazed Media
If your media has already become glazed, there’s still hope. You can restore it by adding an abrasive cleaning powder and running the tumbling machine for a few hours. Afterward, flush the media with water to remove any remaining residue. This method is cost-effective, especially if a large portion of the media has been affected. Regular cleaning can help extend the life of your media and maintain high-quality finishes.
Get in Touch With Finishing Systems Today
Media glazing is a common challenge in surface finishing, but it doesn’t have to be a deal-breaker. With the right strategies, you can prevent it and even restore your media when needed. At Finishing Systems, we specialize in helping businesses achieve consistent, high-quality finishes. Contact us today to learn more about media glazing, or ask us about our products and services. Let us help you improve your finishing processes and meet your quality goals.
Aluminum Die Casting,Aluminum Casting Wheel,Aluminum Alloy Die Casting Parts,Aluminum Die Casting Products
Ningbo Yinzhou Leisheng Machinery Co.,Ltd , https://www.nblscasting.com